Throughout the history of angling there have been only a few revolutions in the making of the very heart of a fishing rod, the blank. Wood, bamboo and split cane, steel and fibreglass have all been used and often to great effect but today the world market is dominated by one material, carbon fibre, also called 'graphite'. While cane and glass rods are still beloved by many, the vast majority of today's anglers will use a carbon fibre rod. The combination of strength, lightness and sensitivity with manufacturing adaptability makes them an ideal choice for almost every niche of this very diverse sport, from delicate fly rods to mighty beachcasters, but when and where did this last revolution take place and who were the men responsible for the very first carbon fibre fishing rod?
The First Carbon Fibre Filaments
This story has its origins in the post-war period when processes for the manufacture of carbon fibre were being researched across the globe. By heating organic fibres, the 'precursor', low-modulus filaments could be created. These ultra-fine, continuous, individual strands of carbon could be combined in their thousands and produced in lengths called 'tows'. Tows could then be woven into a cloth and impregnated with resins to produce …. what? The strength and flexibility of the new material seemed to have enormous potential in numerous industries.
During the 1950s significant research into higher modulus fibres was ongoing in Japan (Tokay Inc.), the U.S.A. (Union Carbide with the U.S. Air Force Materials Laboratory) and in Great Britain (The Royal Aircraft Establishment and Rolls Royce). Each country acted independently and employed different methodologies.
In the United States efforts were focused on producing carbon fibre from rayon, a semi-synthetic fibre made from cellulose and invented by Courtaulds, U.K. in 1905. In 1958, at Union Carbide, Roger Bacon invented a method by which fibres with a 20% carbon yield could be produced from rayon but the process was inefficient and the resulting fibres were of low modulus, lacking both stiffness and strength. They were used as high temperature insulation and in filters. This early, limited success led others in America to pursue rayon as a precursor in the manufacture of stronger, higher modulus carbon fibre and in 1960 Richard Millington with H. I. Thompson Fiberglass Co. produced tows of 99% carbon fibre from rayon by a process which involved 'hot-stretching' to prevent shrinkage. This fibre was suitable for combining with resins to make a composite which was light, strong and could be blended to vary in rigidity and flexibility. However, the rayon-precursor manufacturing methods proved to be very expensive and inefficient with the resultant cost of tow at $1000 - $1500 per kilo.
Simultaneously and independently, Japanese and British research was focused on producing carbon fibre from a different precursor to rayon – polyacrylonitrile or 'PAN'. In Great Britain, Courtauld U.K.'s PAN fibres, 'Orlon' and later 'Courtelle' were also known as 'Special Acrylic Fibre' or 'SAF'.
In the late 1950s Dr Akio Shindo, of the Agency of Industrial Science and Technology in Osaka, part of the then Ministry of Industry and Trade of Japan, demonstrated that using PAN as the precursor produced a stronger material than rayon. His patent was filed in 1959, licensed first to Tokai Electrode and Nippon Carbon, and later to Toray, which was to become Japan’s leading carbon fibre manufacturer. In 1961 he was able to create a 55% carbon fibre yield using a PAN precursor but crucially they could not prevent shrinkage during the process.
Trade ministry subsidy into carbon fibre research continued throughout the 1960s in Japan whilst in both the U.S.A. and the U.K. government funding came via military research organisations; the U.S.A.F. Materials Laboratory, Ohio, and the Royal Aircraft Establishment (R.A.E) in Farnborough, Hampshire, England. With the Cold War and the Space Race in mind, military and aeronautical uses for carbon fibre were at the forefront of development in the West whilst in demilitarised Japan applications within industry and commerce were the focus.
The British Story - The Men at the R.A.E
In the early 1960s William 'Bill' Watt and a small group of colleagues at the Royal Aircraft Establishment, Farnborough, a British Ministry of Defence research facility, tasked themselves with the development of higher modulus carbon fibre tows for composite production.
The Royal Aircraft Establishment scientists were:-
Dr. William 'Bill' Watt, O.B.E., F.R.S. (1912-1985) Senior Principal Scientific Officer, R.A.E. Farnborough.
Leslie Nathan Phillips, O.B.E. (1922-1991) worked in the Plastic Technologies Section.
William 'Bill' Johnson, (1924-1986), joined the R.A.E. in 1954, where he was the Laboratory Assistant and Experimental Officer, later Principal Scientific Officer.
Dr. Roger Moreton, (1935-), a materials scientist awarded a PhD for his research into factors affecting carbon fibre strength.
These four men were the principal British pioneers in PAN-derived carbon fibre technology. In addition, Professor Anthony 'Tony' Kelly, C.B.E., D.L., F.R.S., F.R.Eng (1929-2014), at times assisted the team as a consultant in his field of expertise, resin composites.
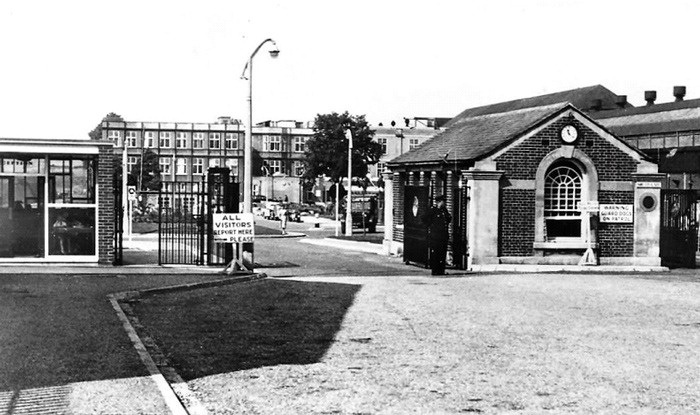
1. The South Gate, R.A.E. Farnborough, Hampshire, circa 1960.
Early Developments
In parallel to the Japanese, the R.A.E. used a PAN precursor, theirs being 'Orlon' supplied by Courtaulds, U.K. and later 'Courtelle'. When oxidised on a frame within a certain temperature range the fibres neither shrunk nor stuck together and in 1964 the R.A.E patented their own carbon fibre manufacturing process producing what became known as 'Type I' tow. (1) This process was later licensed to Courtaulds, U.K., Morganite Modmor and Rolls Royce to manufacture on an industrial scale. Both Rolls Royce and Courtaulds had already been independently pursuing their own methods of manufacture but each abandoned their research in favour of Watt's process.
Rolls Royce later employed the R.A.E.'s process to manufacture 'Hyfil', the carbon fibre composite used in their original RB211 jet engine fan blades for the Lockheed L-1011 TriStar. However, the blade's matrix failed under bird-strike tests and the setback contributed to the company becoming insolvent, leading to its nationalisation in 1971.
Doctor Roger Moreton, a core member of the R.A.E.'s original research team, has recorded extensive recollections of his career, including his time with Watt et al, for the British Library's 'Voices of Science' archive. (2) There, in Part 4, Dr. Moreton recalls buying Meccano from the local toy shop to make the frame on which to wind the fibres and prevent shrinkage on heating – a problem confounding Japanese and American research – thereby paving the way for the R.A.E.'s 'Type I' tow.
In May, 2018, Dr. Moreton, now retired, generously agreed to talk to me about his time working on carbon fibre research at the R.A.E. The toy shop, he remembered, was in Farnham, Surrey. In the early 1960s Meccano was still principally manufactured from metal – few plastic pieces were yet sold – so a frame could be constructed which would resist the heat of the furnace when the precursor was heated. The Meccano frame they built happened to be 6” long – and consequently this was the length of the first low modulus, PAN-derived carbon fibre filaments the R.A.E. produced.
The furnace they used, Dr. Moreton told me, was a Tamann furnace, acquired from Germany in reparations at the end of the Second World War, which heated the PAN fibres to 2500 degrees Centigrade. The resultant fibres were examined to assess their physical qualities and some were then combined with a resin to create a solid composite material which proved both laterally strong and stiff yet relatively flexible and light.
The Atomic Research Establishment, Harwell
In 'Carbon Fibers and Their Composites' Peter Morgan (3) wrote:
“ Courtaulds later developed a special acrylic fiber (SAF), specifically for conversion to carbon fiber. The work at RAE was successful and culminated in Watt, Phillips and Johnson applying for a patent in 1964. ”
“ From these results the RAE developed a small scale laboratory continuous carbon fiber process to demonstrate feasibility. To provide larger quantities for commercial evaluation, a contract was placed in 1965, with the Atomic Energy Research Establishment, Harwell, who had existing furnaces that could be readily adapted for this application and initially, Harwell produced a staple fiber in approximately 4.5 Kg batches some 35 cm long. ”
“ Once the commercial UK companies came on stream, Harwell turned their attention to making continuous fibre "
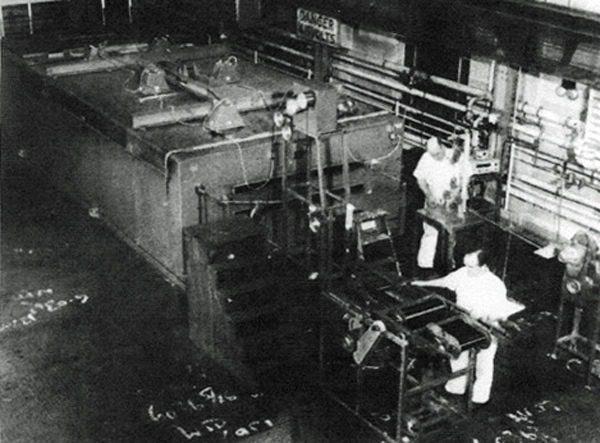
2. Part of the Harwell pilot-scale carbon fibre production plant, circa 1965.
In 'Carbon Fibres By the Ton', Fred Roberts & Dr. Bryan Morris (4), respectively the then head and section leader of the Materials Processing Group at the Atomic Energy Research Establishment, Harwell, give the date for the first contract as late 1965 with two further contracts following in 1966. By the end of that year 150 lbs (68 Kg) of carbon fibre had been produced in the form of tows 14 inches (35 cm) long, however, it had a problem – ''shear strength''
"While composites of fibres in resin having the expected high tensile strength and modulus could be made, they had a low interlaminar shear strength of only 2500 lbs / sq inch. This figure is too low for most applications, and engineers required value of around 10 000 lbs / sq inch. The vital problem was how to achieve a good bond …. between the resin and the fibre. By early 1967 Farnborough had developed a gaseous treatment of the fibres at elevated temperatures which improved bonding.”
During Part 6 of his 'Voices of Science' interview Roger Moreton is asked if there was ever a 'Eureka' moment. He replies:
"Well .... yes .... I suppose the very first time we got the good properties .... The fibres were a quarter of the density of steel, they were twice the stiffness of steel and twice the strength .... It's quite spectacular, really .... sometime between 1965 and 1967, I guess.” (2a)
Simultaneously, Harwell concentrated on chemically cleaning both the precursor and final fibres and so increased the interlaminar shear strength by three-fold. By 1968 the production was being operated on a routine basis.
“Equipment for making continuous type II tow had been set up in the laboratory at Farnborough. During 1967, we modified the Harwell plant to produce continuous lengths of both Type I and Type II carbon fibre on a somewhat greater scale. Early in 1968, priority was given to producing 1000 ft lengths of tow as a fairly routine operation to supply …. the rapidly growing demand in the United States” (4)
'Type II' tow was produced by heating the precursor at 1500 degrees Centigrade and resulted in less stiff, more flexible fibres. Further advantages were lower energy costs and longer furnace life making 'Type II' tow more economic to produce.
Harwell's capacity was limited and in 1967 the National Research Development Corporation, the government agency responsible for commercialising publicly-financed research, licensed the R.A.E.’s technology to three British companies: Rolls-Royce, Morganite Modmor and Courtaulds, U.K. The R.A.E contracted one ton of tow from Morganite and this they supplied by the end of 1967, called 'Modmor I'. So great was its value, around £65,000, it was kept in a locked room known as 'the Black Fort Knox'. Today in 2018 its equivalent value would be around £1.1 million.
It is, I contend, deeply relevant to the history of carbon fibre rod-making that during 1967 'Type I' carbon fibre tow of sufficient length and strength to make a two-piece, 9 ½ ft rod first became available to the R.A.E. and their associated researching companies, including the Moncrieff Rod Development Company and Hardy Brothers.
The Fishermen Came Knocking
In his draft of 'The Strange Tale of how I Met Richard Walker' Leslie N. Phillips, reflecting on his time at the R.A.E., wrote:
"At an early stage in the development of carbon fibre the Ministry of Supply invited the B.B.C. to broadcast an introductory programme. It was transmitted under the title, 'From Strength to Strength' …. ” (5)
'From Strength to Strength: The Search for New Materials' was broadcast on B.B.C.1 on the 2nd of June, 1964 at 9:25 p.m. (6) The programme was made in the hope they could raise awareness of new materials amongst British manufacturers. As an added enticement they offered carbon fibre tows free for experimentation, on the condition that any results obtained be shared with the R.A.E., plus a financial inducement - this at a time when American companies were paying $1000+ per kilo. The programme was viewed with interest by one man in particular, Richard Walker.
''This Happy Band''
Richard 'Dick' Walker (1918-1985) had worked at the R.A.E. during the Second World War where he was assigned to radar research. In 1945 he returned to the family business near Letchworth, Hertfordshire, making agricultural machinery. A keen angler from childhood, he soon established himself in the angling press and tackle industry, inventing an electronic bite alarm, the Arlesey Bomb and, in 1952, he published his first book, 'Rod Building For Amateurs' (7). That same year he landed a 44 pound (20 kg) carp at Redmire pool in Herefordshire which held the British record for 28 years.
One day in 1954 he received a letter questioning his recommendations regarding the 'lift method' for setting a float and replied to the sender in interest. So began a life long friendship between Dick Walker and Fred J. Taylor.
Fred J. Taylor, M.B.E. (1919-2008) was an enthusiastic countryman and author. He wrote 18 books on fishing, shooting, rabbiting, food and travel. He was the first Englishman to receive the Silver Dolphin Award, the highest honour in sport fishing in the United States, and was awarded an M.B.E. for his services to angling in 2008.
Naturally, Walker and Taylor introduced one another to their own fishing pals and soon a group of friends grew into what Fred Buller, a key member, dubbed, ''This Happy Band''. Other members included Peter Thomas, Peter Stone and Leslie Moncrieff.
Fred Buller (1926-2016) served with the Royal Navy in World War II where he was trained as a photographer. Demobbed in 1947, He opened a gun and tackle and photography business, Chubbs of Edgware, London, which soon gained a reputation for quality of service. Through Chubbs he met Walker, Taylor, Moncrieff, Maurice Ingrams, Bernard Venables, Hugh Falkus and Jack Hargreaves amongst many other leading anglers of the day. Buller rose to renown in the 1950's as a successful match fisherman but developed into a true all-rounder, writing and co-writing some of the most influential angling literature of his – and our – time. He was awarded an M.B.E. in the 2010 New Year's Honours List for services to the sport.
At 6' 5” tall Leslie Moncrieff (1913-1986) was known to the angling press as 'The Gentle Giant'. He came to the fore as a champion beach-caster, developing his own 'Lay Back' casting method and, a trained engineer, he designed his own glass fibre 'Springheel' and 'Longbow' rods.
Hardy Brothers, the M.R.D.C. and the R.A.E.
In the mid-1950's James 'Jim' Hardy (1927-2012) joined the illustrious sporting goods manufacturers Hardy Brothers of Alnwick, England, founded in 1872 by his grandfather, William. In 1959 'Mr. Jim' joined the board as Works Director and soon after brought Richard Walker to the company as an advisor on tackle development.
By the late 1950's, having endured the austerity of the Post-War years, leisure fishing in Great Britain had once again become popular and this encouraged a progressive, inventive attitude in the British tackle-making industry. At this time, Moncrieff, Walker, Buller and Taylor were giving free advice to various manufacturers but often enough they found it was being ignored. Inspired by Walker's new relationship with Hardy Bros. they decided to form a company dedicated to tackle innovation.
In 1963 Moncrieff, Walker, Buller and Taylor formed a partnership called the Moncrieff Rod Development Company (M.R.D.C.). They agreed an exclusive arrangement for their services with Hardy and Taylor and Buller immediately joined Walker at Alnwick where they worked on several popular ranges of fibreglass fishing rods. When, in 1964, Dick Walker watched 'From Strength to Strength' on the B.B.C. he recognised the potential of carbon fibre for use in rod making, immediately getting in touch with Leslie Phillips at the R.A.E., a member of Bill Watt's small team researching this technology. At their earliest opportunity Jim Hardy and Dick Walker travelled to Farnborough to discuss using the new material in rod making. Phillips was particularly encouraging about the possibilities.
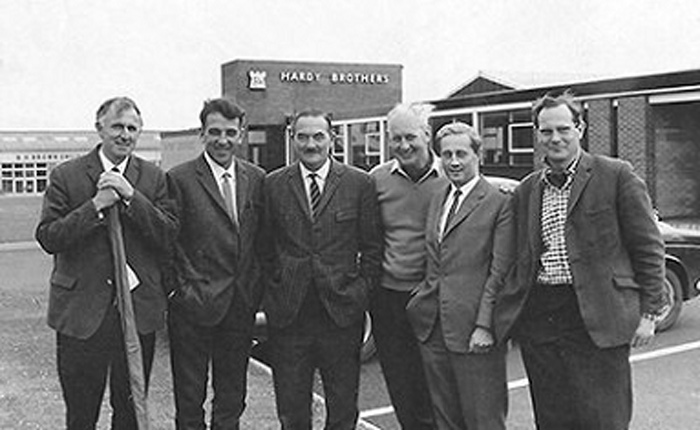
3. Pete Thomas, Fred Buller, Frank Moir, Dick Walker and Bill and Jim Hardy, ext. Hardy Brothers, Alnwick, circa 1968.
The First Carbon Fibre Fishing Rods
Supplied initially with lengths of carbon fibre tow up to 90 cm long (5), Hardy Brothers & the M.R.D.C. set about their research back in Alnwick whilst continuing to develop glass fibre rods for the company. This included weaving the tow into a usable cloth; the analysis of different resins and resin/composite ratios; development of the means to heat and compress the rolled cloth to form a blank or ferrule and the creation of a suitable 'scrim', a base layer upon which the prepared fibre is placed to add 'hoop strength' and prevent crushing under stress. All the time Hardy/M.R.D.C. were researching, tow-length production was increasing at Harwell and commercial manufacture was being prepared by Morganite, Rolls Royce and Courtaulds U.K..
After several stages of unsuccessful development they produced a batch of workable prototype rods. One of these was given to Fred Buller, a 9 ½ foot spinning rod, an account of which can be found at the Angling Heritage Museum's website. (8) These first rods were found to be far too rigid for most uses and Fred's ended up in his cottage in Ireland where it was used to hoick out half a mackerel to tempt big pike. At times it would be offered to guests as a stand-by if they had brought nothing better and there it remained for the next thirty years ….
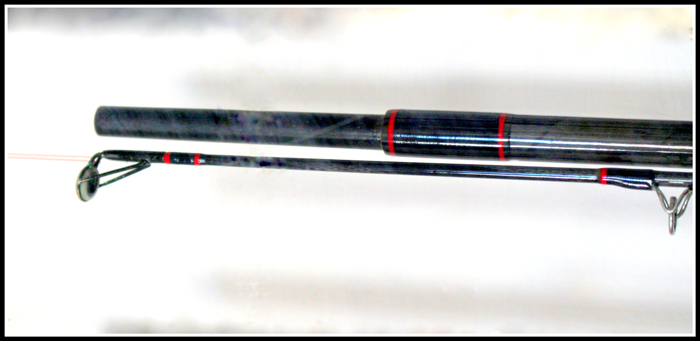
4. Fred Buller's 'Hardy 9 ½' Carbon Spinning': Butt ferrule and tip.
5. Fred Buller's Hardy Prototype Carbon Rod (below, centre).

Problematic Prototypes
There were significant problems with these initial rods. Hardy/M.R.D.C fed their results back to Farnborough where Watts' team analysed them and offered solutions. Leslie Phillips wrote (5):
“Within a few weeks, information began trickling back. The rods, while being both light and powerful, were really too violent in their response; flies were repeatedly snapping off their leaders during the cast.
Evidently, it was time for a re-think. We needed a grade of fibre which was a little less stiff, even stronger, with a higher elongation at the break (the so-called type II fibre).
Happily such a product was already under development in the Department, in the form of a thin but continuous tow. Possibly this could be woven? ”
Phillips continued:-
“Early experiments with a small handloom showed real feasibility; and a contract was placed with James Carr and Sons Ltd. (9), traditional weavers of narrow tapes, to mechanise production.“
Constructed with a loosely stitched, glass fibre weft it produced a beautifully even, strong cloth with flattened carbon warps arranged parallel to each other.
The R.A.E. continued their research through 1968 culminating in Leslie Phillips and the Secretary of State for Defence (as the head of R.A.E.) applying for a British patent on March the Tenth, 1969 titled 'Improvements In or Relating To Continuous Carbon Fibre Tapes'. (10) The improvements described therein include a glass fibre weft to hold the warp in place. When this cloth is rolled the glass weft would contribute much-needed hoop-strength to a tube or cylinder – or rod blank.
It is perhaps worth noting, too, that Leslie Phillips mentions flies being cracked off in the cast, implying that prototype fly rods had been made alongside the surviving spinning rod we have today.
Dating the Hardy 'Carbon Spinning 9 1/2'
We know from Leslie Phillips' and Roger Moreton's personal accounts that they were producing 'Type I' carbon fibre tow from 1964 and attaining small-scale production by 1966 with Harwell's 35 cm length tows. Production was increased and they improved tow length and quality until, by late 1967 to early 1968, Harwell was producing continuous 'Type I' tow with a shear strength of 10 000 lbs / sq inch - tow of a quality and length suitable for the process of rod making.
We know, too, from Phillips and from Roberts and Morris (Harwell), that the more flexible 'Type II' carbon fibre tow was being manufactured successfully by late 1967 with a new patent for improvements being drawn up and submitted in the first quarter of 1969 by Leslie Phillips and the U.K. government. This was the more flexible material Hardy Brothers would subsequently use in their carbon rod research although their commercial rods were ultimately built from Japanese Toray T300 carbon fibre cloth. Phillips' statement above infers necessarily that Buller's prototype rod was constructed from 'Type I' carbon fibre at a time when 'Type II' was ''Happily …. already under development''.
This establishes with some certainty that the Hardy 'Carbon Spinning 9 1/2', the World's first carbon fibre fishing rod, was made between mid-late 1967 and early-mid 1968, i.e. after the production of suitable 'Type I' tow by Harwell and prior to the distribution of Morganite's 'Type II' tow from the R.A.E. in late 1967- early 1968, the material used in Hardy's rod development programme once it became available.
Recognition and Restoration
At the turn of the millennium Fred Buller, realising the historical importance of his old 'dead-bait pike rod', sent it to The House of Hardy Ltd. for refurbishment.
“ The original handle and reel fitting were renovated and the rings, including a folding butt ring seen on many later Hardy beachcasting rods, were rewhipped retaining as much of the original as possible, but bringing the rod back to an “as new” condition.. “ (8)
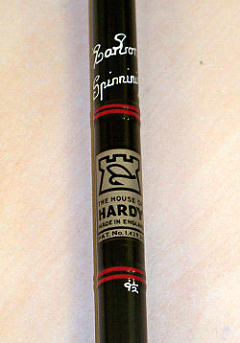
6. 'The House of Hardy' Decals on Fred Buller's Prototype Carbon Rod.
The House of Hardy decals, their logo and a patent number referring to Hardy Brothers'/Richard Walker's carbon fibre reinforced ferrules (11), are not original – Hardy Brothers did not become The House of Hardy until 1985 and the ferrule was not actually patented until 1971 so neither decal could have graced the original, unrestored rod. That so much of the original remains, indeed that any of it remains, is an extraordinary stroke of good fortune.
In 2009, Fred Buller kindly donated the 'Carbon Spinning 9 ½' to the Angling Heritage Museum, Torrington, Devon, where it is now on display to the public.
From Research to Rod Rack
It was, perhaps, fortunate that in 1967 Hardy's financial position improved when they were bought out by the Harris & Sheldon Group. The new chairman, James Miller, saw the value in Hardy's owning their own blank-rolling facilities and sought assistance from J. Kennedy Fisher, Inc., a well-established American producer. By 1968, Hardy Brothers had begun the process of creating their own fibreglass manufacturing factory in Alnwick, a subsidiary company called 'Fibatube', which would roll their own rod blanks and later supply to the trade, too. In the mid-1970's production was diversified to include carbon fibre blanks and in 1992 glass fibre blank production ended completely. Carbon fibre dominated the market.
For Hardy Brothers, Ltd. the transition from 'Type I' prototypes to commercial production proved difficult. Encouraged by improvements in the action of 'Type II' rods Walker, Phillips and William Frederick Hardy applied for a patent in the name of Fibatube in March 1970. (12) In the patent description Walker wrote (p.2):
“Preferably the carbon fibre reinforcement comprises from 2% to 25% of the total volume of the blank, with the remainder comprising glass fibre reinforcement and cured resin.”
Stating a specific percentage in Hardy's patent proved an expensive and unnecessary mistake. Rival companies successfully produced rod blanks with carbon fibre contents outwith Hardy's announced parameters thereby obviating the patent's legal restrictions and opening the floodgates. As the technology advanced rods of 96% graphite were produced in the U.S.A. and Hardy Brothers began to loose ground.
Their 1971 ferrule patent highlights a difficulty they had struggled to overcome; that of strengthening any joints in a rod sufficiently enough to withstand the rigours of repeated casting stress. Consequently, it was not until 1974 that a new high strength carbon fibre spigot ferrule was used on a Hardy fibreglass rod and 1975 before they were promoted in the Hardy catalogue.
That same year Hardy brought out their first carbon fibre rod - 'The Hardy Graphite' range of spinning rods (13). A range comprising the 'Graphite Carp' and five new fly rods were introduced in their 1976 catalogue, four in the 'Graphite' series (71/2', 8', 81/2', 9' from #3 - #10 weight) and the 'Richard Walker Farnborough' (9', #7/8) designed by Dick Walker, named as a tribute to the men of the Royal Aircraft Establishment whose work had been instrumental in changing the world – and the world of fishing in particular.
7. Hardy 1976 catalogue, Graphite Fly and Dick Walker 'Farnborough'.
American and Japanese Progress
While early American research at Union Carbide using rayon as a precursor had proved unsatisfactory, on the 25th of May, 1968, Great lakes Carbon filed a patent titled 'Process for the manufacture of continuous high modulus carbon yarns and monofilaments'. This patent cites :
“SUMMARY OF THE INVENTION These and other objects which shall become apparent in the course of the detailed description of the invention that shall be made, have been accomplished by a two stage process in which PAN fiber yarn or monofilament is first stretched beyond commercial textile practice to obtain maximum orientation and tenacity and is then subjected to a partial oxidation while being maintained under tension. The partially oxidised material is then formed into skeins and subjected in this stress-free state to a further oxidation, followed by carbonisation in a nonoxidising atmosphere to the desired temperature maximum which can provide any carbon fiber within the range of maximum strength to maximum modulus. “ (14)
They state using ''a type G Courtelle 1 yarn, marketed by Courtaulds Ltd. '', the same yarn the R.A.E. were experimenting with in the U.K. at the same time.
In Japan the pioneering work begun in Osaka by Dr. Akio Shindo had been continued by Toray Industries, a company with a historical record of innovation in synthetic fibres. In the late 1960's Toray successfully developed a precursor that was far superior to anything seen before and in 1970 they signed a joint technology agreement with Union Carbide, bringing the United States back to the forefront in carbon fibre manufacturing. Dr. Shindo was granted a patent licence and the U.S.A. finally got economical access to a standard modulus graphite cloth, Torayca T300, producing 12 tons in 1971. Soon after, Hercules, Inc. joined Union Carbide and Great Lakes Carbon fabricating graphite cloth primarily for use in the aerospace industry. Production to the R.A.E. patent was started in 1971 by Hercules, Inc. (who had an arrangement with Courtaulds Ltd.) and Morganite Modmor, Inc., a joint company formed by the Whittikar Corp. and Morgan Crucible.
Fenwick: From Golf Club Shafts to Fishing Rods
One early recreational use for graphite was as a composite for making golf club shafts and in the early 1970's one such ended up in the hands of Don Green and Jim Green at Fenwick.
Fenwick of Westminster, WA, are an American tackle manufacturers who, while in Kent, WA, in the 1960's, established a reputation for excellence building glass fibre fishing rods. Jim Green was their production manager and Don Green (no relation) their master rod-builder. Already expert in fibreglass rod blank rolling, they were immediately curious about this new material and set about experimenting with it.
The result was what is widely acknowledged to be the world's first commercial graphite fishing rod, the 'High Modulus Graphite' (HMG) spinning rod range, which debuted in 1973. Fly models followed the next year. Technically, ''High Modulus' was a bit of an exaggeration but the HMG rods were certainly of a higher modulus than their glass contemporaries.
8. Fenwick 1975 catalogue, HMG Baitcaster.
By 1975 they had taken the lead in carbon / graphite rod technology from Hardy. In order to create sufficient strength in their rods, particularly towards the tip, Hardy chose to increase the amount of glass scrim used. This tended to make their rods top-heavy in the hand and slow in their action while American manufacturers were able to make rods just as strong but lighter, crisper and of smaller diameter. These offered less wind resistance in the cast and proved more popular with the consumer.
The HMG range was not without its problems. Like Hardy, Fenwick found that the stresses of practical use often proved too much for their rods and they would break but they went to market anyway - often to the frustration of their customers. Fenwick though, for all their problems, had won the carbon rod race and while Hardy delayed entering the market Fenwick improved their rods 'on the hoof'.
The Graphite Revolution Begins
Other American rod makers quickly adopted and adapted to graphite cloth. In 1973, Gary Loomis, then with Lamiglas, Woodland, WA, handled one of these prototype Fenwick rods at the AFTMA show in Chicago and was extremely impressed. He obtained cloth samples from Hercules, Inc. through researchers with Boeing, Seattle, resulting in his '96% Graphite' rods introduced to the market in 1974. Whilst heavier than Fenwick's 'HMG' they were less liable to break. However, anglers aware of Fenwick's difficulties had become wary of the new material. Loomis recalls:-
“That entire first year we debuted the rods I wasn’t trying to sell rods – I was trying to sell graphite!“ (15)
The Shakespeare Company of Columbia, SC, had been working with graphite since the late 1960's, manufacturing golf club shafts amongst other things, and inventing the Howald Process for manufacturing carbon fibre male ferrules (with titanium female ferrules) in 1967. By the early 1970's they had developed their own prototype rods and by 1973 were supplying The Orvis Company of Vermont with 'Graphite' blanks during the brief period in which Orvis converted its blank-making facility from fibreglass. These rods reached the market in 1974. Shakespeare's own 'Graphlite' range were introduced in 1975.
J. Kennedy Fisher, who had assisted Hardy Bros. in establishing their Fibatube factory, also turned to graphite production, supplying Winston and Scott with blanks by 1975, amongst many others in the trade.
As in the U.K., over the following decade fibreglass rod production continued in America but on a declining scale until, like cane before it, it became a niche market with only ardent fans continuing to enjoy its qualities. Graphite fishing rods had become ubiquitous.
In Conclusion
While initially relatively expensive, carbon fibre rods proved both popular with the consumer and easier to work with than glass. The result was that production costs soon fell and their popularity soared. Their strength, lightness and versatility in design and purpose changed the face of angling forever.
Hardy's failure to adequately qualify their 1970 patent had opened the market to others. This error saw them fall behind in the race to commercially market the new medium in rod-making and the U.S.A. and Japan came to dominate the industry for the following quarter of a century. More lately they have been superseded by South Korea and the People's Republic of China who lead production today, often under contract to the major Western tackle companies to roll blanks to their specific designs, sometimes still using high quality Japanese Toray graphite.
Sadly, Roger Moreton's feelings about fishing and carbon rods weren't entirely positive. He was a keen kayaker and in the final instalment of his recorded memoirs complains about having to avoid the new, really long carbon fishing rods he'd helped to invent:
".... and they cost the earth! Well they seemed to to me. I did find that a bit irritating .... because I thought, if I were a fisherman I wouldn't have felt it was worth spending the money." (2b)
But thousands, then millions of anglers did think the product was worth the price. Leslie Nathan Phillips wrote:
“Somewhere in the archives of the Materials Department at the R.A.E. is our last letter from Richard Walker. In it, he says that the development of carbon fibre and its application to fishing rods “saved the British tackle industry”. A fitting memory to a thoroughly nice man.“ (5)
Phillips also recalled a day when Richard Walker spoke to him in a personal vein:-
“I was, he said, too tense and serious, evidently I had been working too hard; and what was required was a day-off to go fishing!
Although taken aback at first I soon fell in with the suggestion …. I found myself being rowed across Grafham Water as his guest.
During the next few hours of fishing, he gave me a demonstration with the leaded nymph and the sinking line that was masterly …. He rarely missed a fish."
A few days later, Richard wrote the proceedings in his column in a low-key style. He reported that he had fished with the co-inventor of carbon fibre at Grafham and ''we both caught trout to two pounds in weight''. Reading between the lines, it was a perfect day! “ (5)
Doubtless, there have been countless more since, thanks to this ''spectacular'' innovation.
James Barlow.
June, 2018.
References:
1) G.B. Patent number 1110791: 'The Production of Carbon Fibres'.
https://worldwide.espacenet.com/publicationDetails/originalDocument?CC=GB&NR=1110791A&KC=A&FT=D&ND=3&date=19680424&DB=&locale=en_EP
2) The British Library's 'Voices of Science' archive, 'Roger Moreton: An Oral History of British Science'. Part 4 focuses on his time with Watt at the R.A.E. The British Library's 'Voices of Science' archive, 'Roger Moreton:An Oral History of British Science. Part 6: a) 75 mins 12 sec ff. / b) 40 minutes 30 sec ff.
https://sounds.bl.uk/Oral-history/Science/021M-C1379X0049XX-0006V0
3) Peter Morgan
'Carbon Fibers and Their Composites': pp. 73-80.
https://books.google.co.uk/books?id=wUhuBwAAQBAJ&pg=PA72&lpg=PA72&dq=
William+Watt+of+the+Royal+Aircraft+Establishment&source
=bl&ots=7eiZC9PtQZ&sig=1vcrZbgPo3cW7Nrhdo8ShyEvuwY&hl=en&sa=X&ved=0ahUKEwiK8pqc-aXZAhXkKMAKHS9yBWUQ6AEISTAJ#v=onepage&q=
William%20Watt%20of%20the%20Royal%20Aircraft%20Establishment&f=false
4) Roberts & More
'Carbon Fibres By the Ton', New Scientist and Science Journal, 08/11/1970, p.68,
https://books.google.co.uk/books?id=zmgH-LFPPa0C&pg=PA68&lpg=PA68&dq=harwell+carbon+fibre+manufacture&sourc
e=bl&ots=yzTwI7QTp8&sig=tM64pgjDdSKtd_8HI3KiHv9DQXo&hl=en&sa=X&ved=0ahUKEwiXv5TEk4XbAhXLIsAKHUqCA-gQ6AEIWzAI#v=onepage&q=harwell%20carbon%20fibre%20manufacture&f=false
5) From a draft of 'The Strange Tale of how I Met Richard Walker' by Leslie N. Phillips, held by the
Angling Heritage Museum, Torrington, Devon. Note: Phillips refers directly to ''the Ministry of Supply''. However, this ministry was dissolved in 1959 being replaced by The Ministry of Aviation. The March 1970 'Fishing Rods and Processes for their Manufacture' patent refers to ''The Secretary of State for Defence (formerly Minister of Aviation Supply)”. This ministry was dissolved in 1967 and is that to which Phillips refers.
http://www.anglingheritage.org/
6)
Genome.ch.bbc.co.uk – 'From Strength to Strength'.
http://genome.ch.bbc.co.uk/45622a5447734de0a5debb4ed7865d87
7)
'Rod Building For Amateurs' by Richard Walker, 1952, Belfield and Bushell. Kent.
8)
'The Birth of a Rod', anglingheritage.org.
h
ttp://www.anglingheritage.org/p-8882-the-birth-of-a-rod.aspx
9) James Carr and Sons, Ltd., of Clarence Mills, Clarence Street, Chester Road, Hulme, Manchester.
10) G.B. Patent Number: GB1260955 (A) – 'Improvements In or Relating To Continous Carbon Fibre Tapes'.
“Priority number(s):
GB19690012448 19690310
1,260,955. Carbon fibre tape. DEFENCE SECRETARY OF STATE FOR. 3 March, 1970 [
10 March, 1969; 6 Nov., 1969], Nos. 12448/69 and 54452/69. Heading D1K. [Also in Division C1] A carbon tape contains a plurality of parallel aligned carbon fibres functioning as warp members, the members including for example carbon fibre tows and a continuous weft thread is woven through said warp members at a frequency between 2 and 10 threads/ inch, said weft thread serving to maintain the warp threads in parallel alignment. The warp threads may be composed entirely of carbon fibre but preferably include bundles of glass fibres in an amount up to 90% by weight of the warp. The carbon fibres used may be high strength high modulus carbon fibre. The weft thread may be carbon fibre but is preferably a glass fibre which may comprise 1 to 10 filaments. The carbon fibre used may have, before such use, have been treated with resin, and the tape when formed may be impregnated with resin. The tapes referred to are such that they may be used to form fibre reinforced articles by being wound on, or applied to a former, impregnated with resin if required, and cured.“
https://worldwide.espacenet.com/publicationDetails/biblio?II=1&ND=3&adjacent=true&locale=en_EP&FT=D&date=19720119&CC=GB&NR=1260955A&KC=A
11) Jim Hardy, 'The House the Hardy Brothers Built', p.122. Pub: The Flyfisher's Classic Library, 1998.
12) G.B. Patent Number: GB1351732 (A) – 'Fishing Rods and processes for Their Manufacture'. Filed 19 March 1970.
"We have now discovered that the rate of return, after deflection of the rod, plays a significant part in obtaining improved performance of a fishing rod, and that the use of carbon fibre reinforcement improves the said rate of return.
A fishing rod may be made having solely carbon fibre as reinforcement to a cured resin matrix and this would be suitable if a very stiff and strong rod is required but in most cases we have found that a better rod is produced if carbon fibres are selectively positioned within the body of a fishing rodhaving another reinforcing fibre such as glass fibre in a cured resin matrix."
https://worldwide.espacenet.com/publicationDetails/originalDocument?CC=GB&NR=1351732A&KC=A&FT=D&ND=3&date=19740501&DB=&locale=en_EP#
13) Dick Walker.co.uk at Hardy's website: See charts for rod model release dates. Please note: some dates conflict with Hardy's catalogues.
http://dickwalker.co.uk/hardy.html
14)
U.S. Patent for Great Lakes Carbon - 'Process for the manufacture of continuous high modulus carbon yarns and monofilaments.'
15)
TackleTour interview with Gary Loomis, 2009, part 1, p.2
http://www.tackletour.com/reviewinterviewgaryloomispart2.html
Images:
1: – 'South Gate, RAE Farnborough' – From a Frith Ltd. postcard, courtesy of Mr. Mike Charlton (
Aviationpostcard.co.uk).
http://www.aviationpostcard.co.uk/
2: – 'Part of the Harwell pilot-scale carbon fibre production plant' - New Scientist and Science Journal, 08/11/1970, p.68.
3: - 'Pete Thomas, Fred Buller, Frank Moir, Dick Walker and Bill and Jim Hardy ext. Hardy Bros' – copyright
Angling Heritage.
http://www.anglingheritage.org/
4, 5 & 6: – 'Fred Buller's 'Hardy Carbon Spinning 9 ½' – copyright
Angling Heritage
http://www.anglingheritage.org/
7: - Hardy 1976 catalogue Graphite Fly – copyright Pure Fishing UK Ltd.
8: - Fenwick 1975 catalogue HMG Baitcaster – copyright Fenwick, U.S.A.
Acknowledgements:
With grateful thanks for their assistance and encouragement to:-
Dr. Roger Moreton, Keith Armishaw, Brian Taylor, David Norwich, Alan Brown (FAST Library), Mike Charlton and the members of
The Fly Fishing Forum U.K.
https://www.flyfishing.co.uk/vintage-and-collectable-tackle/408309
-happy-50th-birthday-carbon-graphite-rods-brief-history-formative.html